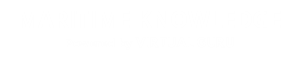
Working Principle of :
1) Centrifugal Pump
Centrifugal pump is a roto-dynamic pump applying a centrifugal action and the liquid receives energy from the impeller due to its continuous rotation. The fluid moves radially with increasing velocity which is converted into pressure in the volute casing.
In other words, with the mechanical action of an electric motor or similar prime mover, the rotation of the pump impeller imparts kinetic energy to the fluid through centrifugal force. The fluid is drawn from the inlet piping into the impeller intake eye and is accelerated outwards by the impeller vanes to the volute casing and outlet piping. As the fluid exits the impeller, if the outlet piping is vertically upwards, the fluid kinetic energy is converted into static pressure to allow flow.
If the outlet piping is open at a lower level (horizontal or vertically downwards), the fluid will be released at greater speed.
A centrifugal pump works by converting kinetic energy into potential energy measurable as static fluid pressure at the outlet of the pump. This action is described by Bernoulli's principle. Centrifugal pumps are used for large discharge through smaller heads.
The power required to drive a pump (Pi), is defined simply using SI units by:
Single Stage Radial Flow Centrifugal Pump where:
Pi is the input power required (W)
ρ is the fluid density (kg/m3)
g is the standard acceleration of gravity (9.80665 m/s2)
H is the energy Head added to the flow (m)
Q is the flow rate (m3/s)
η is the efficiency of the pump plant as a decimal
Components of a Centrifugal Pump:
Impeller: The rotation of centrifugal pump impeller causes the liquid it contains to move radially out wards from the centre to beyond the circumference of the impeller.
Volute casing: The casing is known as volute casing because of its spiral shape. The casing section collects the liquid, discharged by the impeller and converts velocity energy into pressure energy
Stuffing box: Stuffing box (Gland Packing) has the primary function of protecting the pump against leakage at the point where the shaft passes out, through the pump casing.
Mechanical seal: A mechanical seal is fitted in the seal / bearing housing (the point where the shaft passes out, through the pump casing) preventing leakage of fluid being handled by the pump.
Bearing: Bearing transfer the shaft’s load and provide rotary relative movement minimizing the friction between the members. Bearing are usually roller bearing or ball bearing if externally located (as ingress of water will cause irreversible damage to the bearing) or else brass bush / sleeve if internally located.
Coupling: Coupling is used to connect the pump shaft to the prime mover shaft. Mostly flange or jaw type coupling are used. Coupling bolts are fitted with a rubber sleeve to provide a cushioning effect on the bolts due to high starting torque and high speed of rotation.
Wear rings: To minimize the cost of pump maintenance, centrifugal pumps are designed with wear rings. Wearing rings are replaceable rings that are attached to the impeller neck and pump casing with a small running clearance of 0.2 mm as illustrated (Maxm allowed = 1.0 mm) between the wear rings on the impeller and the casing. Operational wear due to corrosion and cavitation attack results in the wear down of this component which needs to be replaced periodically thus prolonging the life of the impeller and the casing.
2) Reciprocating Pump:
Reciprocating pumps are self priming positive displacement pumps.
Application on board these days in restricted to:
a) Engine room bilge pump gear driven with an electric prime mover
b) Steering compartment bilge pump operated by hand or pneumatic device
c) Stripping pumps in cargo pump room (steam operated)
A reciprocating pump essentially consists of a piston and a cylinder where the piston is enclosed in the cylinder. The cylinder is connected to suction and delivery pipes, each of which is provided with a non-return or one way valve called suction valve and delivery valve respectively. The function of non-return or one way valve is to admit liquid in one direction only. Thus the suction valve allows the liquid only to enter the cylinder and the delivery valve permits only its discharge from the cylinder. The piston is connected to a crank by means of a connecting rod. The piston is equipped with ebonite rings that act as a sealing component with the cylinder.
As the crank is rotated at uniform speed by a prime mover, the piston or plunger moves to and fro (or backward and forward) in the cylinder. When the crank rotates from e = 00 to e = 1800 the piston which is initially at its extreme bottom (that is, it is completely inside the cylinder), moves to its extreme top, (that is, it moves outwardly from the cylinder). During the outward movement of the piston a partial vacuum (pressure below atmospheric) is created in the cylinder, which enables the atmospheric pressure acting on the liquid surface in the well or sump below to force the liquid up the suction pipe and fill the cylinder by forcing open the non return suction valve.
Since during this operation of the pump the liquid is sucked from below it is known as its suction stroke. Thus at the end of the suction stroke the piston is at its extreme top position, the crank is at e = 1800 (i.e. at TDC), the cylinder is full of liquid, the suction valve is closed and the delivery valve is just at the point of opening. During the downward (forward) stroke delivery of fluid takes place with the suction valve in closed position.
3) Screw Pump:
Screw pumps fall in the category of rotary positive displacement pumps. Screw pumps are different from other rotary pumps because of the axial flow of the fluid through their pumping elements. The fluid in screw pumps moves between the screw threads and are displaced axially as the screws rotate and mesh.
Due to the axial flow pattern and low internal velocities, the screw pumps have certain advantages in applications where churning and agitation of fluid is highly objectionable or not desired as in the case of LO circulation. The inter-meshing of the screw threads on the rotors and the very fine clearances with the surrounding casing creates a seal between the pumps inlet and outlet.
Due to the rotation of the screws and its axial movement cavitations pockets are formed in the helices of the screw. As the screw moves the pockets also move axially and act similar to a piston moving in one direction, while the fluid is moved axially from inlet to outlet.
Application on board: Sludge pump, Main Engine LO pump, Cargo Oil pumps.
4) Gear Pump:
Though the construction, shape and design of gear, vane and globe pumps are a bit different, they fall under the same category of rotary positive displacement pumps. The working of all these pumps is based on the same principle, i.e. pumping of the liquid with the help of rotating elements. The rotating elements can be gears, screws or vanes.
A gear pump’s rotating assembly consists of two gears, a driving gear and a driven gear. Pumping in a gear pump takes place when the driving gear meshes with the driven gear to form cavities that moves the fluid. The cavities are the clearances between the gears or lobes and the body of the pump. The mating surfaces of the gears meshing provide continuous sealing between the inlet and outlet ports.
As the rotation of the pump continues, movement of the cavities progresses, moving the fluid along the way. After some time, a point is reached where the seal between the captured fluid and the outlet part of the pump is broken. At this point of time the vanes, gears or lobes, forces the volume of the captured fluid out of the pump. A continuous cycle takes place due to the simultaneously opening of new cavities at the inlet port. This leads to a continuous flow of liquid though the suction and discharge ports.
Application on board: Oil Transfer Pumps for various on board applications.